Technological evolution in recent decades has opened the door to previously unknown possibilities, revolutionising the world of work. Today, for example, in precision engineering workshops, machining operations are completed using CNC (Computer Numerical Control) machines capable of simplifying and speeding up processes while drastically reducing the margin of error.
But what are number control machines? How do they work? In this article, we will go into this question, dwelling on the aspects that need to be known in order to understand these state-of-the-art working tools.
What are CNC Machines?
Numerically controlled machines are machine tools controlled by mechatronic measurement and control technology, or computers. In this sense, their movements and functionalities are set in advance, by means of specific software, so that the machining process or production of precision engineering products is automated.
As we shall see in the next few lines, the intervention of the operator is limited, whose task is 'only' to supervise the process, intervening where the computer is unable to understand the instruction received.
CNC Machines in Precision Engineering Workshops
Due to their guaranteed high efficiency, CNC machines are widely used in various fields of mechanics, such as the metalworking or manufacturing industry or in carpentry, tailoring, upholstery, upholstery, packaging and more.
In precision workshops, where it is essential to ensure very high standards of quality, they are of different kinds: there are CNC milling machines, drilling machines, CNC lathes, press brakes, punching machines and CNC welding machines.
Starting from raw materials (be they metal, plastic, iron or G25 cast iron), they allow cutting, welding, marking and the production of sophisticated products with extremely durable characteristics.
The History of CNC Machines
The first numerically controlled machines appeared on the Italian scene around the 1940s and 1950s, with the aim of taking advantage of the innovative turn to automate machining.
Although far removed, technologically, from modern specimens, these machines made it possible to speed up production practices and satisfy a large number of requests. Soon, however, the CNC machines were upgraded with analogue and digital computers, resulting in what we know today.
How CNC Machines Work
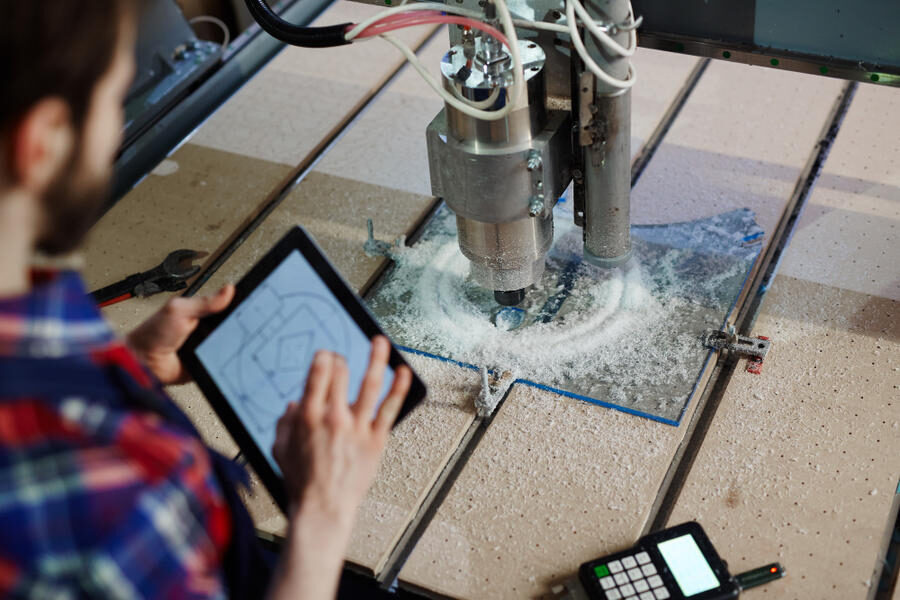
To understand how CNC machines work, we need to introduce their anatomy. Compared to traditional tools, they mount:
- Encoders: these can be either linear or rotary. Their job is to inform the on-board computer of the movement and position of the axis on which they are mounted.
- Electric motors: required to control the movement of the axes
- Drives: special units that control the movement of motors
- Axes: The number of axes is what distinguishes CNC machines from conventional ones. Classified as X,Y and Z, they respectively represent the three dimensions (width, height and depth) in which the operation can be performed. In reality, the number of axes varies depending on the machine and ranges from 5 axes, to 8, to 10 up to 24
- Computer: this is the heart of CNC machines, the unit that controls the entire machine. Through software, it receives directives from the operator (coded using a standardised language called G-Code or ISO Code) and executes the work
In principle, numerically controlled machines work in a rather simple way: the skilled operator communicates all the necessary instructions to the computer to finalise the precision mechanics product or third-party machining, which, in turn, interacts with its mechanical and digital organs to make it real.
Despite being reduced, the technician's task is crucial: without him, and his initial instructions, the machinery would not be able to function, and it is his responsibility to ensure that no corrective actions need to be taken during the machining process.
The Advantages of Numerically Controlled Machinery
There are many impressive benefits provided by CNC machines. The first is obviously the greater productivity they are able to guarantee compared to manual machines. Accompanying this is the speed of execution and the punctuality offered for the manufacture of each product, such as clamping systems.
Thanks to the computerised brain, the CNC machines do the work in (almost) autonomy and allow the margin of error to be reduced to a minimum. The results are always of the highest standard and each item is characterised by high quality precision.
The other advantages of CNC machines are:
- Remote control of the machining process
- Extreme efficiency in grinding, milling, drilling, turning and other machining operations
- Repeatability of machining operations
- Flexibility and adaptability to various materials (stone, metals, G25 cast iron, textiles, synthetics, etc.)
- Agility and greater degree of freedom thanks to the axes
- Extremely short machining times
- Cost efficiency and economy across the entire productivity range
- Increased operator safety
Bonanomi, a precision engineering shop founded in 1946, also has a large fleet of state-of-the-art CNC machines and a team of specialised technicians. In this way it is able to meet the requirements of the world's largest tool manufacturers, ensuring that every machining operation complies with DIN standards.